Breakthrough
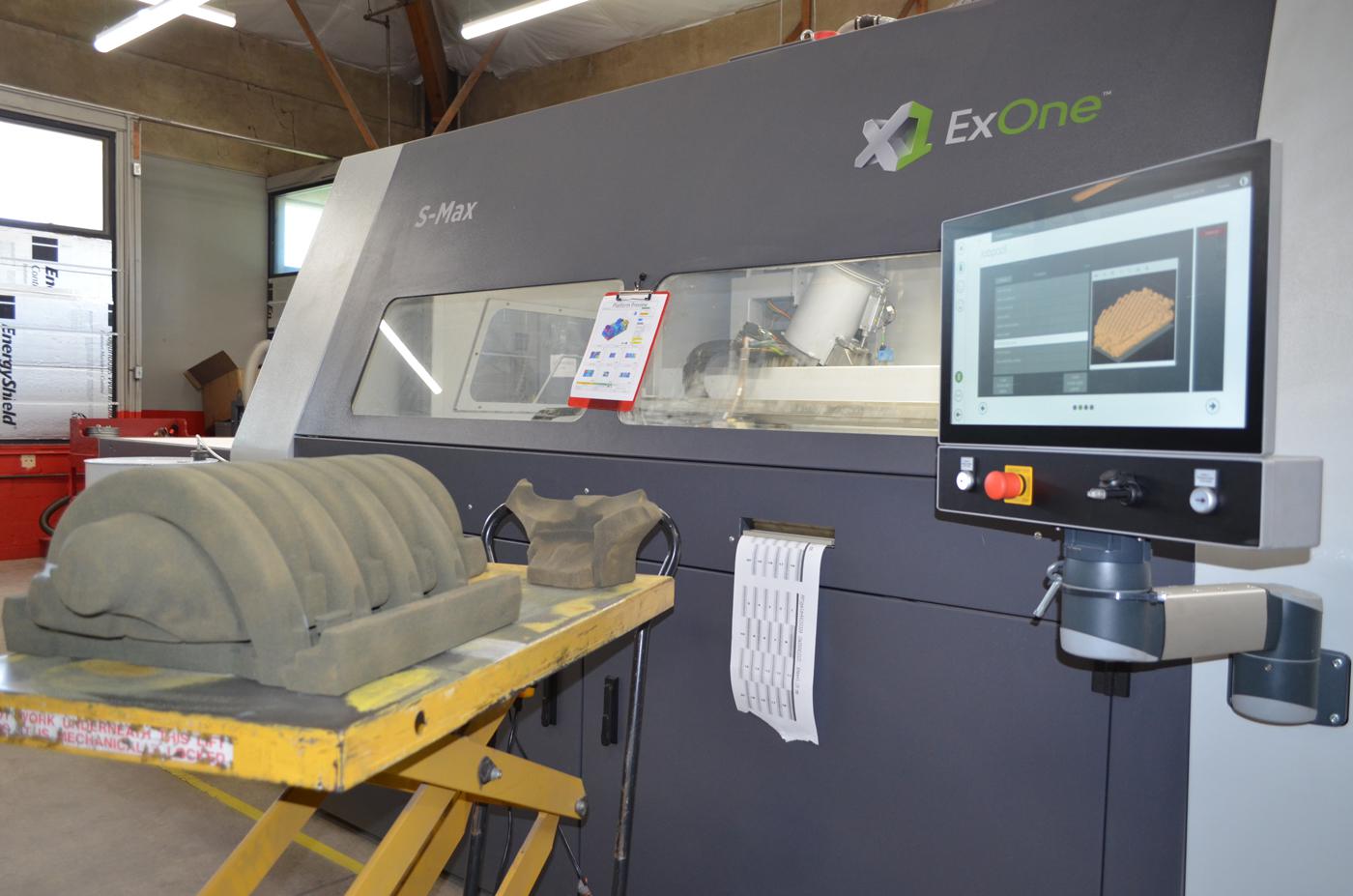
The current generation of performance intake manifolds is benefiting from 3D printing and advanced composite materials.
Additive manufacturing, which includes the more commonly known 3D printing technology, is starting to make an impact in the production of intake manifolds designed for racing and high-performance applications.
For years, manufacturers have used 3D printing to construct thermoplastic prototypes for fitment and design review. Some teams put these prototypes on a flow bench and even tested them on the dyno with a running engine. For some projects, other prototypes were 3D printed in metal for additional testing and possible end use in select applications.
However, the prospect of using 3D metal printers for mass production was never seriously considered. While there are unique design possibilities using 3D printing, the costs and manufacturing time keep the technology in the development phase or for one-off, end use only by high-end race teams.
That doesn’t mean 3D printing isn’t finding a way into the foundries where popular aftermarket intake manifolds are cast. Some manufacturers are using 3D printers to make the cores that are used to define the air and coolant passageways in the interior of the intake. The impact is likely to be quite significant for racers.
“Now that we’re able to do more with the 3D cores, we expect more performance,” said Brent McCarthy of Edelbrock, Olive Branch, Mississippi.
“It takes everything that we’ve had in the past and fixes everything that we’ve found wrong,” added Mark Fretz of Brodix, Mena, Arkansas. “Everything we’ve learned over the years with porting and doing different things to a manifold, we’ve incorporated all of that into this new manifold. It makes a big power difference.”
Also making news on the manufacturing front is the continued growth of composite and billet aluminum materials.
“Using carbon fiber for the plenum saves weight and reduces heat soak, compared to a full billet manifold,” said Caleb Newman of Performance Design, Auburn Hills, Michigan. “Also, the plenum is universal and can be used across eight different applications.”
“The billet manifolds are much more into play now,” said Jeff Jones of 1 Way Technologies, Washington, Indiana. “There’s a lot of development in billet-type manifolds.”
“Prototyping is the biggest area of change; with solid modeling programming and billet capability you can deploy faster prototypes,” confirmed Scott Highland of Dart Machinery, Warren, Michigan.
Since the intake manifold is a critical tuning factor in the performance of an engine, designers are always experimenting with the dimensions and shapes that affect airflow into the cylinders. There are pressure-wave dynamics, resonance, heat management, and other factors that play into their choices. Occasionally, established beliefs are challenged.
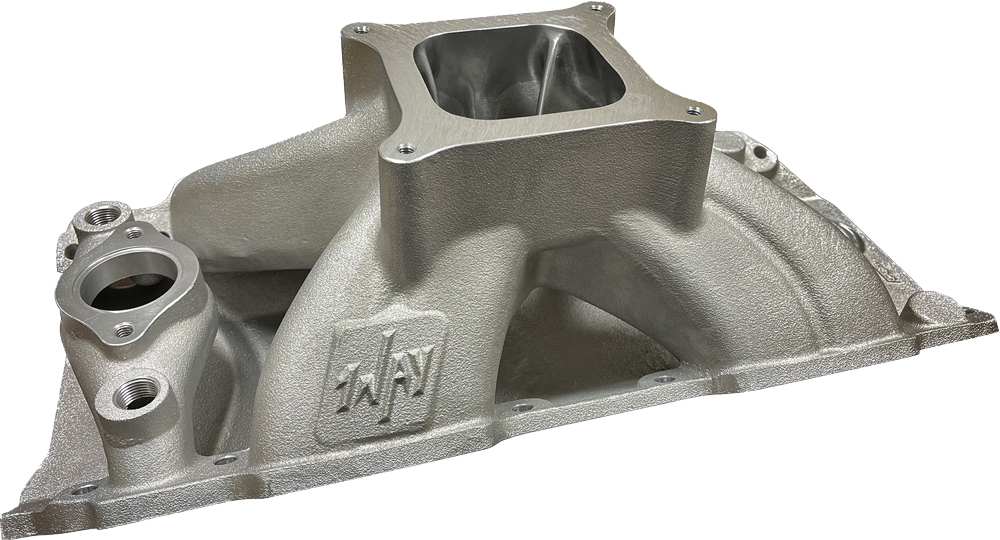
“I’m building two other manifolds that go off the theory of longer and bigger. It’s against the conventional theories, but it really has worked,” said Mike Weinle of Weinle Motorsports, Cleves, Ohio.
For much of the industry, however, it’s keeping up with the demand that really hasn’t let up since the pandemic years. Manufacturers say the supply chain and labor issues have settled, and the main priority now is filling orders and addressing the market demands with an eye on the future.
“Dart is seeing more demand for EFI manifolds driven by boosted applications and nitrous,” said Highland. “Dart is evaluating demand for these various applications with more information to come.”
“We’re still selling a lot of small block Chevys, and the marine manifold does well,” said Bill Mitchell of Bill Mitchell Products, Edgewater, Florida. “Also, Ford manifolds have been picking up lately.”
Building with Sand
The quiet manufacturing revolution at the foundries is still the leading headline as the aftermarket embraces new technology where it is most feasible. The Edelbrock foundry in San Jacinto, California, has recently invested more than $1,000,000 in a new process to 3D print sand cores and molds.
An intake manifold uses different types of tooling for each manifold casting. Every intake starts with a cope and drag plate to create the green sand mold for the outside of the manifold. There are two types of core boxes to build the hard sand cores for the air and coolant passages. The first is the shell core process, where the box, constructed of iron, is heated up and filled with core sand. After the loose sand is poured in the box, the box is rotated, and as the core box moves, the binder in the sand contacting the hot iron solidifies, creating a smooth and uniform ‘shelled’ exterior surface.
“The only problem is, you do have to accommodate in the design that ability for the core box to pull apart and the core to come out, and that involves draft,” explained McCarthy. “That’s basically a series of wedged angles so that when you pull the core out there’s nothing dragging on it. Sometimes the draft is natural, like when a runner has a roof that is ‘laid-over’ compared to the floor. But it can get tricky near the divider walls and at the port exits.”
The Isocure is a similar process where the sand mixture with a binding material is blown into a cold core box. If loose pieces are incorporated into the design, this method can be a little more forgiving with the draft requirements.
“You’ll see that some of our intake manifolds that use shell cores, especially single-plane racing manifolds, the eight-runner set will be assembled from different cores. One core will make four runners, and another core box will make the other four runners, or sometimes two more sets that make two runners each, and each has to be set aside and then glued together. Finally, the joints are dressed up with what we call a mudding process,” said McCarthy. “Our Super Victor 2 uses the more advanced Isocure process, with loose pieces, so the divider walls can be much thinner in the manifold. This allows us to sneak in more runner cross-section area at the plenum.”
But both core processes are time consuming and have draft requirements. When Edelbrock introduced the ExOne 3D printer to the foundry, draft requirements were no longer an issue.
“We can make a core that starts out wide at the bottom, gets narrow in the middle, and wide at the top, or stack runners vertically, and print it in one piece,” McCarthy said. “You could do anything. There’s zero draft requirements.”
The ExOne printer, like any new technology, takes time and experimentation to adopt. Edelbrock has conducted extensive research into the media used by the printer, as it had to be compatible with the casting process. The surface finish left by the cores in the casting is slightly different than the traditional methods.
“We’ve done dyno testing back-to-back with shell core and 3D-printed cores, and we’ve verified the performance is the same or better,” said McCarthy.
Currently the 3D-printed cores are used in less than 5% of the overall intake manifold production, but it is a full-time project to grow that number. The Gen III Hemi intakes are using the process, as are some EFI intakes, and some big block Chevy Victors.
“We have approved it for 10 other manifolds so far,” added McCarthy, noting that the shell core process works fine for dual-plane intakes, but the design possibilities are greater for single-plane performance intakes.
“We’re working on a manifold that’ll be introduced to PRI, and I don’t want to talk about the application,” said McCarthy. “The outside of the manifold will be normally drafted for the cope and the drag plates. But the inside will only be using 3D cores. Again, the nice part is, we haven’t had to worry about draft. We’ll have really nice divider walls on it.
“It also opens the opportunity, if you’re just printing cores and they both fit within the same cope and drag, you can vary the core a little bit and have another part number,” continued McCarthy. “In other words, if you wanted to build a slightly larger runner set, or a slightly larger port exit set, you could go ahead and print 25 cores and run 25 manifolds that have that feature. Where if you’re going to set up an iron core box or Isocure, you want to run a full run of 400, all the same way. That will be exciting, especially in racing manifolds.”
3D Printed Core
When Brodix developed a new 18-degree cylinder head for big block Chevys, a new intake was also needed. To manufacture this new intake, Brodix implemented 3D-printed cores instead of traditional molding sand in core boxes.
“The 3D-printed cores are more precise,” said Fretz. “It’s more time-consuming and more expensive. But performance-wise, it’s a huge advantage. We can pour the manifold just like a ported manifold coming out of the box. You don’t have to do any touch-up to it. There are no parting lines, no imperfections.”
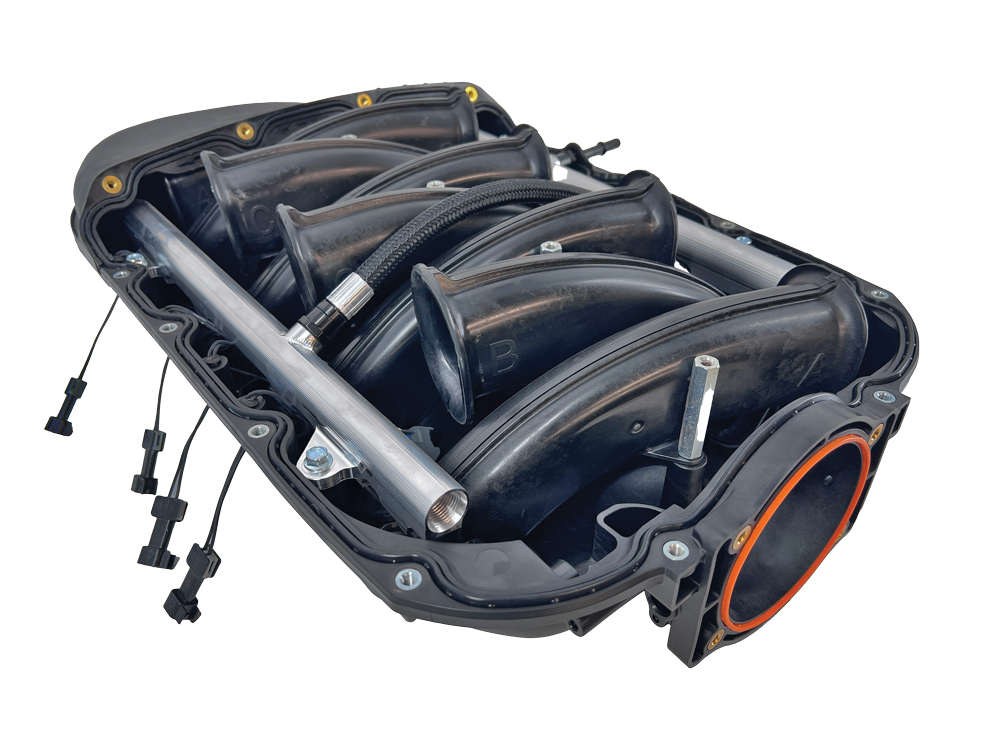
Right now the popular application is likely high-end bracket racing with engines sporting displacements around 600 cubic inches or more.
“The head platform will translate over to tractor pulling, but in the current available program it’s set up more for drag racing,” said Fretz, noting that some unique disciplines like big block modifieds may see this combination, too. “This technology is just for the intake. We still do the traditional core box for all the cylinder heads because they’re CNC ported. So you’re cutting the design into the aluminum. Where on the intake manifold, it’s a lot harder to do. We’re trying to get the intake to come out of the box where it’s really nice.”
This intake is also cast in a fashion in which it can be machined to fit other Brodix heads. “It’s the same intake, but we can machine it for three different heads,” said Fretz. “We put in enough material that we can machine the intake face and the bolt-hole location to fit our new 18-degree conventional, the SR20-style cylinder head, and the Brodix Head Hunter.”
The 3D-printed core intake has been in development for about a year. A test engine was built at the end of 2023, and the printed core manifolds were installed in January. The engine’s owner won a race first time out.
“He went extremely fast, and it’s extremely consistent,” said Fretz. “They ran it in the spring and then built a second engine to continue testing before the manifold was released. Engine builders that have used it have loved it.”
Billet-Focused
Over at 1 Way Technologies, dirt late models, Super Late Model, and Northeast big block modifieds are keeping them busy. There’s more attention paid to billet products with increasing emphasis on software programming to improve design and manufacturing. These billet intakes will be a two-piece design.
“That’s to get around some of the curvatures that you have to deal with in a single four-barrel intake,” said Jones.
1 Way cylinder heads are popular in sprint cars, so the company works closely with fuel injection suppliers to match those intakes with their heads. “Typically, Kinsler or Engler will make something to our specs for our head, and a lot of it is billet,” added Jones.
Sanctioning body rules sometimes drive new product development. A nostalgia drag race series requires a specific cylinder head that 1 Way provides, so there have been discussions about designing and casting a compatible and rules-friendly intake manifold. “It would be target-specific. We’re still waiting on some things there from the sanctioning body before it’s a go-ahead. But they’ve actually approached us so that they can have a little more control of what guys are doing,” said Jones.
As far as trends, Jones does see longer intake runners on single four-barrel applications. “They are getting taller. Guys are trying to optimize the end cylinders versus the middle for better distribution. That’s one of the things that we’ve done, spent quite a bit of time just trying to get middle runners and end runners more even,” he said.
The company is also keeping an eye on the future with a goal of controlling more of its manufacturing.
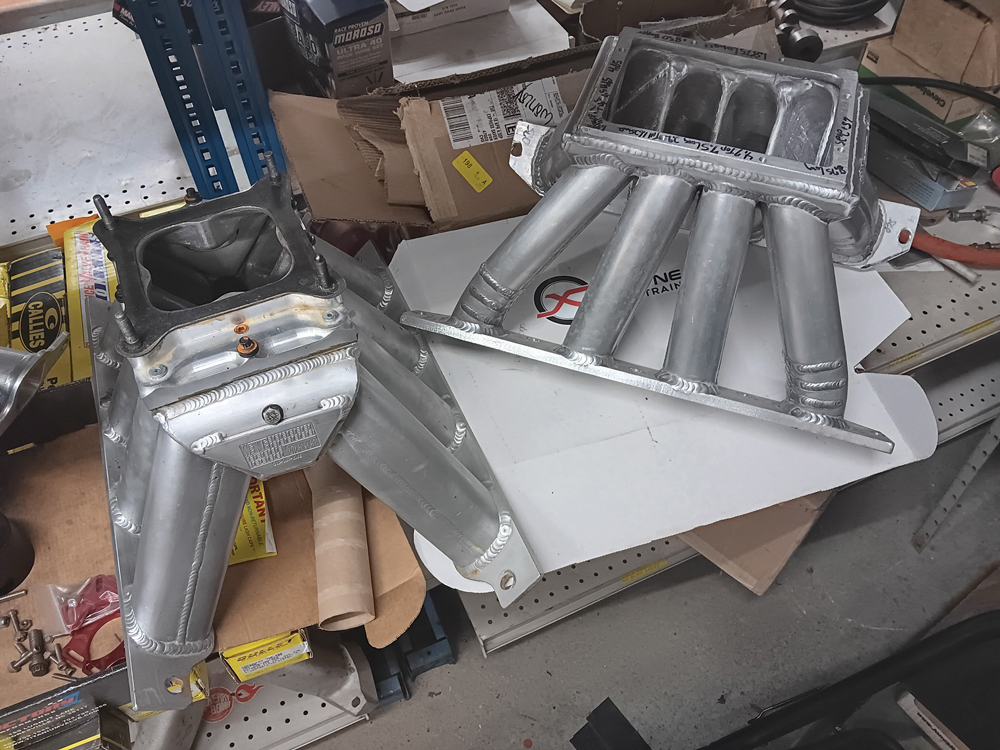
“Just having the ability to do more tooling of our own, the patterns. The kind of stuff where we can actually control our destiny a little better versus relying on other manufacturers to make changes to what we want to do,” said Jones. “3D printing is definitely something that would be in the future for sure.”
Focused On Composites
Manufacturing innovations have been a significant part of Performance Design’s strategy in developing new intake manifolds, especially ones designed to work with forced induction.
“Composites are pervasive in our product line,” said Newman. “Our first product, the Carbon XR, was full carbon fiber runners and plenums with billet aluminum flanges. With our sister company, MPI, we have steadily been increasing our use of polymer composites, namely PA6 with 30% glass fill, to continue to allow new designs, integrated features, and lower cost. We are also implementing OE-level seal design and stackup across all our products.”
Performance Design and MPI can cast PA6 GF30, which is a type of polyamide 6 plastic reinforced with 30% glass fiber, in-house. The process is similar to injection molding, but it can tolerate thick-thin sections better and is more thermally stable.
“To back up the manufacturing, we have developed an in-house pressure pulsation test cell that can cycle a peak boost to full vacuum in seconds at hot and cold temperatures, typically 0–100 degrees C,” said Newman. “To fully validate our Carbon TRc manifold for track abuse and cycles, we have developed the plenum and posts to withstand 50,000 cycles from full engine vacuum to 30 psi boost at 100 degrees C chamber temperature. After passing this test, we did another 5,000 cycles at 60 psi with the same temperature. We thermal cycle test all our seals and gaskets and conduct ultimate burst testing to OE automotive industry standards on top of the typical performance testing on the dyno.”
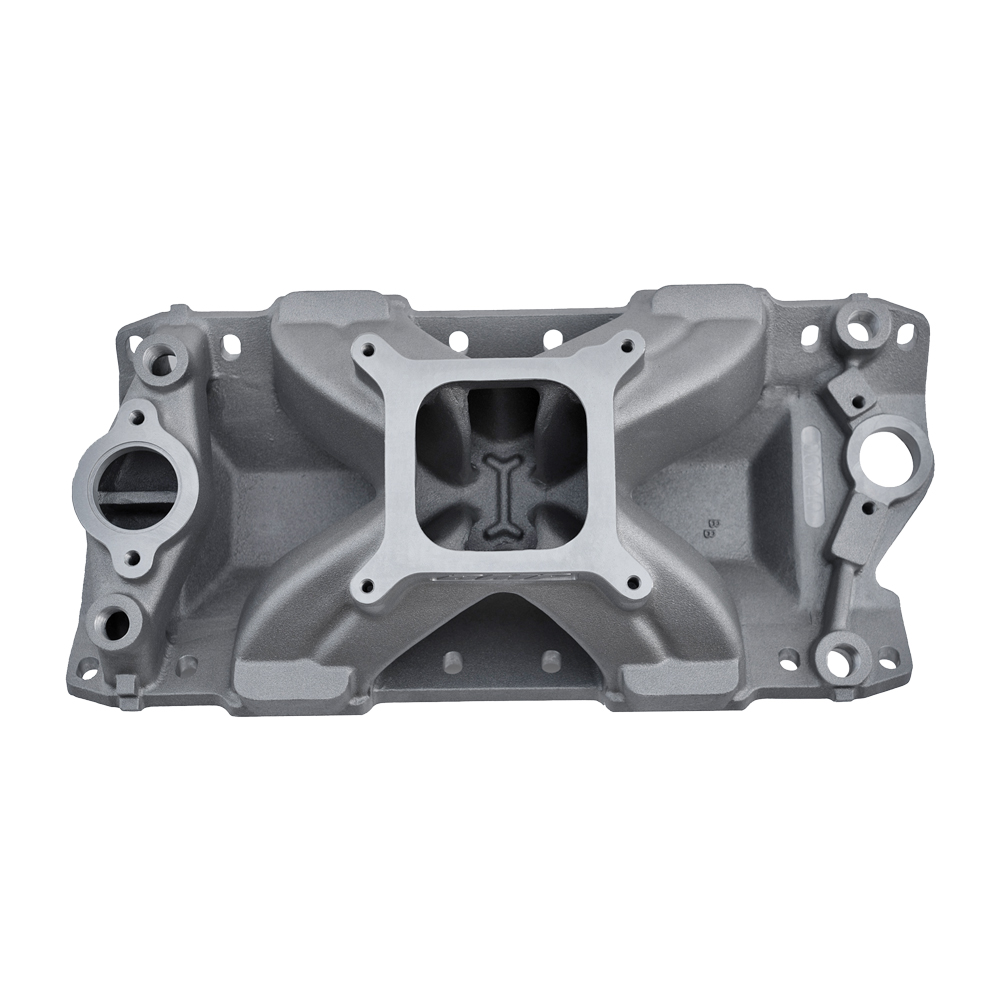
In addition to manufacturing breakthroughs, Performance Design continues to test tuning theories by altering the lengths of the intake runners. “We have a unique in-house coupling of dynamic CFD [computational fluid dynamics] and what we call acoustic tuning. We’re looking at the three-dimensional resonance inside the manifold where all the port and plenum geometry interacts,” said Newman. “We couple that with dynamic CFD to develop most of the actual flow details of the runners, the plenum, etc.
“I am a strong proponent of raised bells with a generous elliptical entry. Coordinating some testing with Edelbrock on boosted variants of our Carbon pTR manifold, we found boost applied to our raised bell architecture far exceeded the gains from boosting a competitor’s tangential bell entrance,” explained Newman. “I have seen this over testing for decades…but we’ve been able to more easily apply the design technique when using polymer and carbon. We are starting to see some of the cast manifolds implement raised bells, so we assume they are seeing the same in testing.”
Proving Theories
Weinle is also working with a similar dynamic, although his development is trial and error, combined with studying theories, and making a bunch of fabricated-aluminum intakes. Most of his efforts target the dirt late model class.
“It looks like the intake charge is too short,” said Weinle. “So, I gathered all the theories on the third and second pulses in the engine.”
With each new manifold, Weinle would increase the runner length a half inch. “And it kept making more power,” he said. “Then I designed one with less plenum and a bigger runner, and I had the fastest car. The engine broke, so I’ve been idle since then. I’ve built two more intakes with the same theory: longer and bigger runners.”
Weinle is confident in the direction he’s taken, so he’s building a carbon-fiber version of the latest intake. “I’m still experimenting, but I’ve found that you can go a lot bigger than most people think you can.”
SOURCES
1 Way Technologies
1way-tech.com
Bill Mitchell Products
billmitchellproducts.com
Brodix
brodix.com
Dart Machinery
dartheads.com
Edelbrock
edelbrock.com
Performance Design
performancedesign.com
Weinle Motorsports
weinlemotorsports.com